Program 3. Processing and Recovery
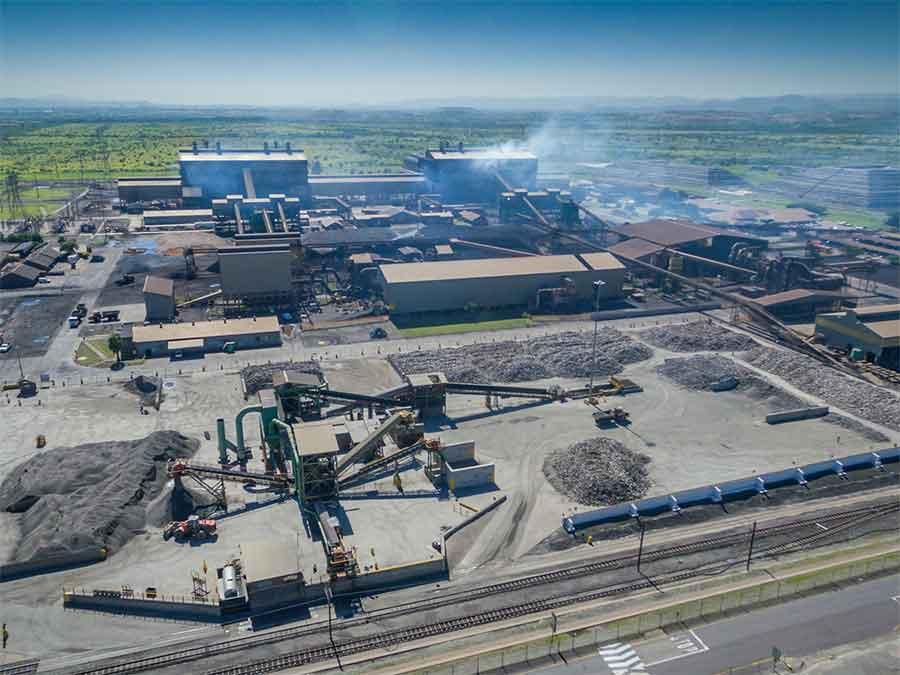
New techniques for optimisation and sustainability.
Critical minerals are mined in one of two ways:
- as primary products(such as REEs and lithium)
- as by-products (such as indium from zinc concentrates, or cobalt from copper and nickel ores) in the production of other minerals.
Many critical minerals are not being processed optimally, or significant opportunities are not being recognised because of poor understanding of critical mineral deportments.
The Processing Program aims to fully realise the value of production of Australia’s rich endowment of critical mineral resources. Our researchers have a strong history of providing research that is commercialised by industry.
The centre has strong links with UniSA’s Future Industries Institute, which hosts excellent, complementary expertise in areas including optimising process performance, reducing energy and water usage, and introducing technological innovations across the resources value chain, and in the following scientific areas of expertise:
- Froth flotation/physical separation/hydrometallurgy
- Surface analytical characterisation of real plant slurries and applications of synchrotron science
- Agglomeration/granulation/pelletisation
- Flocculation, sedimentation, rheology dewatering and process water quality/effects.
-
Research questions
- How can we process ores economically to generate saleable products?
- Can we adapt existing processing circuits to recover valuable by-products that currently report to waste/tailings?
- What are the most efficient ways to process ores with less energy and water resources?
- What are the gaps in capabilities of domestic smelters and refineries to process critical minerals, and how can we close them?
- Can we compete with foreign suppliers, and if so, how?
- How can we ensure mining and mineral processing is environmentally and socially responsible?
-
Research goals
- Define the geometallurgy and geochemical behaviours of critical minerals from ore to products
- Invent and adapt processing strategies and allied technologies to economically extract critical minerals
- Develop alternative processing methods, including bioprocessing, that use minimal energy, water and chemical resources, and that move towards zero waste
- Develop methods to remove non-target metals from valuable ores and concentrates.
-
Centre expertise
- Detecting and managing radioactivity in all types of materials
- Understanding and removing radionuclides from ores and concentrates
- Sensing and scanning technology
- Separating non-target elements from ores
- Advanced sensing, data analytics and machine learning to monitor operations, maximise value and reduce costs
-
Example projects
Superior processing of copper-uranium ores
The minerals in South Australia's copper-uranium deposits present as very fine intergrowths, making it difficult to achieve high purity copper concentrates for market. The ARC Research Hub for Australian Copper-Uranium (2015-2020) is developing and testing new, cost-effective ways to remove non-target metals from copper concentrates from ores in South Australia and beyond.
Partners: BHP, OZ Minerals, SA Government, Australian Department of Defence Science and Technology, Flinders University, Monash University, The University of Queensland
Lean processing for complex resources
The SA Government-funded Integrated Mining Consortium (2018-2022) is using machine learning, sensors and data analytics to develop tools that integrate the entire mining value chain. It is focusing on solutions for complex ore processing, which are typically energy and capital intensive and requires high-cost processing to separate minerals from non-target elements.
Partners: BHP Olympic Dam, OZ Minerals, ASTC, Boart Longyear, Bureau Veritas, Consilium Technology, Datanet, Eka, Magotteaus, Manta Controls, Maptek, Sandvik, Scantech, SRA Technology, ThermoFisher Scientific, UniSA.
Next generation workforce in integrated mining
The ARC Training Centre for Integrated Operations for Complex Resources (2020-2025) is delivering the vital enabling tools needed to integrate and optimise mining, while providing training opportunities for promising scientists. Expected outcomes include improved productivity in mining, strengthened METS sector, and upskilled workforce.
Partners: BHP, Petra Data Science, Orica, Boart Longyear, Bureau Veritas, Magotteaux, OZ Minerals, CRC ORE, Eka, Dassault Systemes, Manta Controls, Datanet, RoqSense, SA Government, AMIRA, Mets Ignited, Rockwell Automation, Scantech, UniSA
-
Key contact